- Per le produzioni BB e NNPB
- THD (dispositivo di altezza tubo) e PAC (controllo della regolazione del plunger) integrati
- Movimento completo del plunger a corsa completa in NNPB
- Stazione di pesatura integrata per BB
Automazione
La struttura stratificata dell’automazione Bottero stabilisce i suoi pilastri fondamentali sui sistemi di controllo (E-Pack Serie 700 Series), i dati e le misurazioni che caratterizzano la linea di produzione. Dati e misurazioni vengono raccolti, organizzati, consolidate e archiviati in un middleware intermedio denominato Process Data Integration Hub. In cima a questo livello, i controlli di primo livello (Tier 1) implementano le loro funzionalità gestendo specifiche sotto-fasi del processo produttivo (DFS, controllo del peso goccia per BB, controllo del movimento, controllo movimento plunger ecc...). Il sistema di automazione del processo rappresentato dalla BoX coordina i controlli Tier 1 e implementa le funzionalità di automazione di processo, con l'obiettivo di controllare e stabilizzare l'intero processo di produzione. Passando dal basso verso l'alto, i dati vengono manipolati ed elaborati per estrarre le informazioni sul processo.
Piattaforma di automazione integrata Bottero
- Standardizzazione completa dei componenti HW, dei moduli SW e delle interfacce di comunicazione
- Unica piattaforma di sviluppo integrato che mette insieme:
- Controlli a circuito chiuso di primo livello (DFS, GWC per BB, Servo Pistone, Valvole Proporzionali 2.0, MWM)
- Controlli di processo a circuito chiuso (BoX)
- Controlli a circuito chiuso di primo livello (DFS, GWC per BB, Servo Pistone, Valvole Proporzionali 2.0, MWM)
- Controlli di processo a circuito chiuso (BoX)
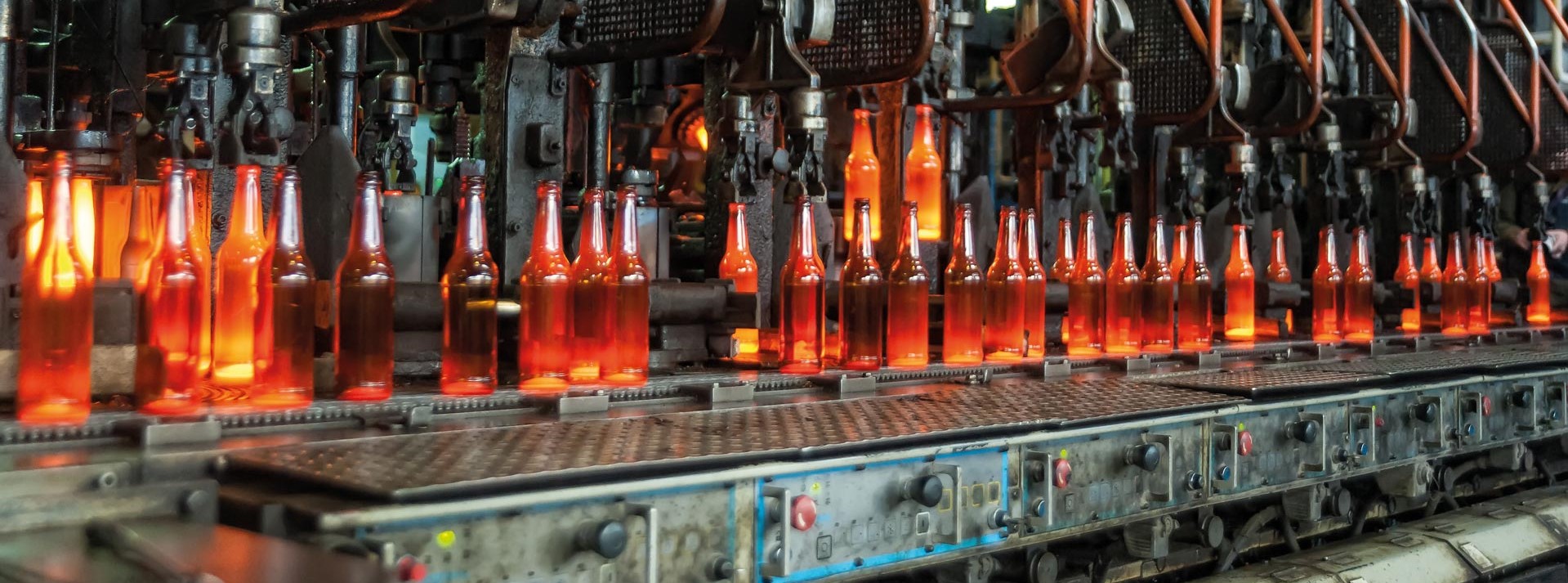
Servo Plunger integrato con DFS
Sistema per la regolazione automatica del profilo di pressata (durata e livelli di pressione) delle valvole proporzionali che controllano il movimento del plunger per le produzioni PB, con lo scopo di:
- Equalizzare e mantenere stabile il profilo di movimento di ciascun meccanismo del plunger per ridurre al minimo il difetto del contenitore.
- Mantenere stabile il tempo di pressata richiesto per ottenere comportamenti omogenei in ambienti dinamici
- Evitare sovrapressioni durante la fase di plunger up
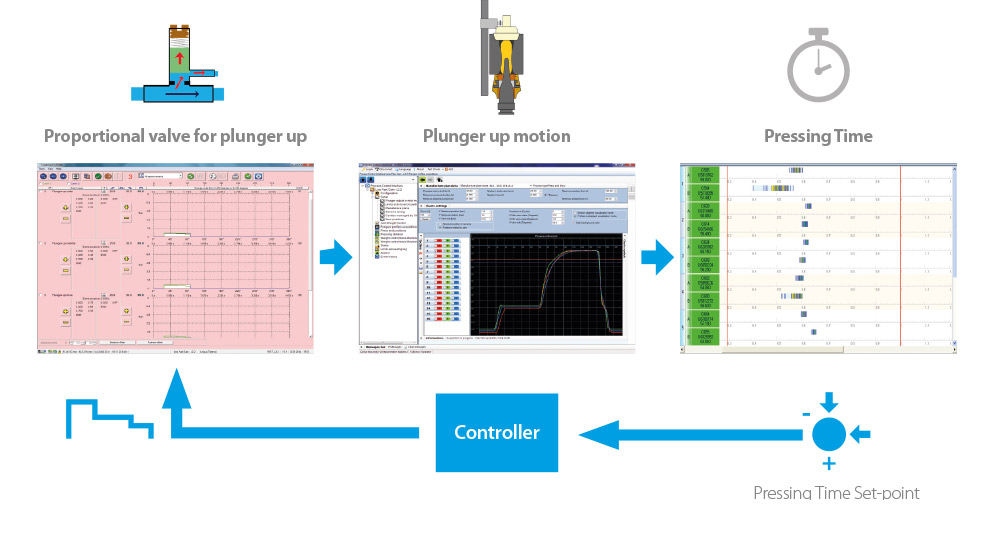
Valvole Proporzionali Bottero 2.0
- Circuito chiuso sulla pressione di uscita in base ad un sensore dedicato
- Due tipi di valvole
- Possibilità di configurare elettronicamente il tipo di valvola (portata o pressione)
- Retrofit meccanico completo con le basi esistenti
- Stessa interfaccia operatore con controllo elettronico
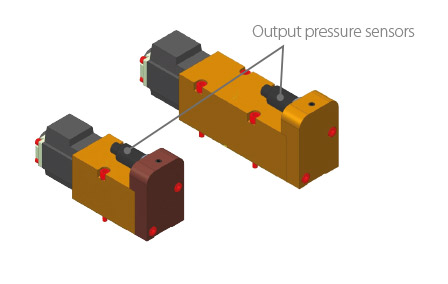
Applicazione Multi Weight Manager
- Strumento di supporto alla messa a punto e controllo delle produzioni con articoli a peso multiplo
- Plug-in opzionale dell'alimentatore per Servo Feeder
- Il peso variabile della goccia si ottiene regolando i parametri del punzone dell’Alimentatore Servo.
- Capacità di compensare il fenomeno dell'accumulo di vetro dovuto alla traiettoria di ritorno
- Le bilance commerciali possono essere integrate opzionalmente per l'acquisizione automatica del peso
- Lo strumento può interagire con L’HOT MASS di Tiama un sistema di telecamere che misura la velocità e il volume della goccia mentre cade, con l’ obiettivo principale di regolare automaticamente il peso della goccia e per controllarne la forma. Questa integrazione offre notevoli vantaggi rispetto alle altre soluzioni:
- Non è necessario pesare manualmente le bottiglie prodotte
- Nessuna perdita di produzione dovuta alla pesa manuale
- Possibilità di impostare produzioni multi-peso (a livello di Feeder) mentre altri operatori cambiano attrezzatura in officina per le nuove produzioni. In questo modo, non appena la macchina è pronta per la produzione,l’impostazione multipeso della goccia è già in esecuzione.
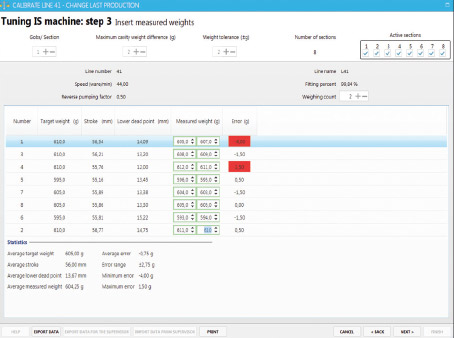
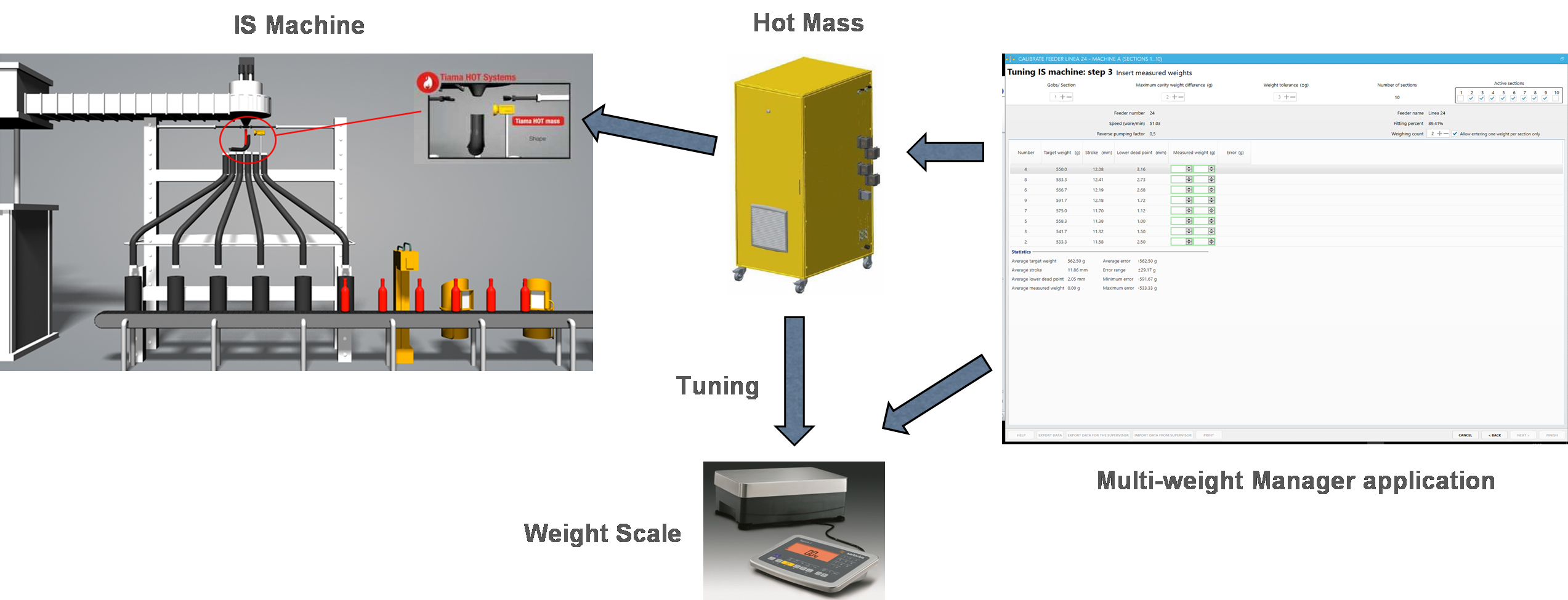
Controlli di processo a circuito chiuso
Il ''controllo di processo cloose loop rappresenta un passo evolutivo chiave: dai controlli di primo livello 1 (incaricati di controllare i sottoprocessi) ai sistemi che guardano al processo di formatura da una prospettiva di livello superiore, di cui BoX è un esempio unico, mettendo i contenitori prodotti al centro dei processi di misura al Hot-End.
Osservando una linea completa di produzione del vetro cavo, dal batch ai pallettizzatori, l'elemento essenziale per il controllo è il processo di formatura: la padronanza del processo di formatura è fondamentale per poter controllare l'intera linea di produzione.
La piattaforma Box
Piattaforma di automazione che implementa funzioni di monitoraggio dei processi e funzioni di automazione correlate a :
- Controllo automatico e ottimizzazione della spaziatura degli articoli
- Controllo automatico e ottimizzazione della distribuzione verticale del vetro (VGD)
Evoluzione del concetto di BoX
La tabella di marcia verso un modello predittivo del processo produttivo

Analisi dei grandi dati
L'approccio Big Data ha lo scopo di analizzare misure e dati per imparare il comportamento ottimale del processo, in particolare:
1. Identificare i parametri chiave del processo che influenzano maggiormente i risultati finali in termini di:
- Correlazione tra le misure dei dati HE (dati di goccia e bozza, misure IR, ....)
- Caratteristiche geometriche dei contenitori (peso, forma, verticalità, ecc.)
- Distribuzione dello spessore del vetro
- Principali difetti
2. Scoprire la correlazione ottimale tra i dati e le misurazioni HE e CE.
Machine Learning: definizione del modello di processo
Il sistema di controllo di processo riceve come input i dati HE e implementa correzioni automatiche alle impostazioni della macchina IS, secondo i parametri del modello di correlazione provenienti dall'analisi dei Big Data.
Non appena sono disponibili le misure CE, il Machine Learning regola e ottimizza tali parametri del modello in base alle caratteristiche dinamiche dell'ambiente operativo.