- For both BB and NNPB productions
- Integrated THD (Tube Height Device) and PAC (Plunger Adjustment Control)
- Full stroke plunger motion tracking in NNPB
- Integrated Weighing Station for BB
Automation
The layered structure of the Bottero Automation Architecture sets its fundamentals pillars on control systems (E-pack 700 series), data and measurements characterizing the production line. Data & measurements are gathered, organized, consolidated and stored into an intermediate middleware called Process Data Integration Hub. On top of this layer, Tier 1 controls implement their functionalities managing specific sub-phases of the production process (DFS, Gob Weight control for BB, Plunger Motion Control, etc...). The process automation system represented by the BoX coordinates the Tier 1 controls and implements process automation features, with the target to control and stabilize the whole production process. Moving from bottom to top, DATA are manipulated and processed to extract process INFORMATION.
Bottero Integrated Automation Platform
- Full standardization of HW components, SW modules and communication interfaces
- Unique, integrated development platform putting together:
– Supervisory platform with open interface toward external Systems
– Wide configuration capability of timing special cycles - Tier 1 close-loop controls (DFS, GWC for BB, Servo Plunger, Prop. Valves 2.0, MWM)
- Process view close-loop controls (BoX)
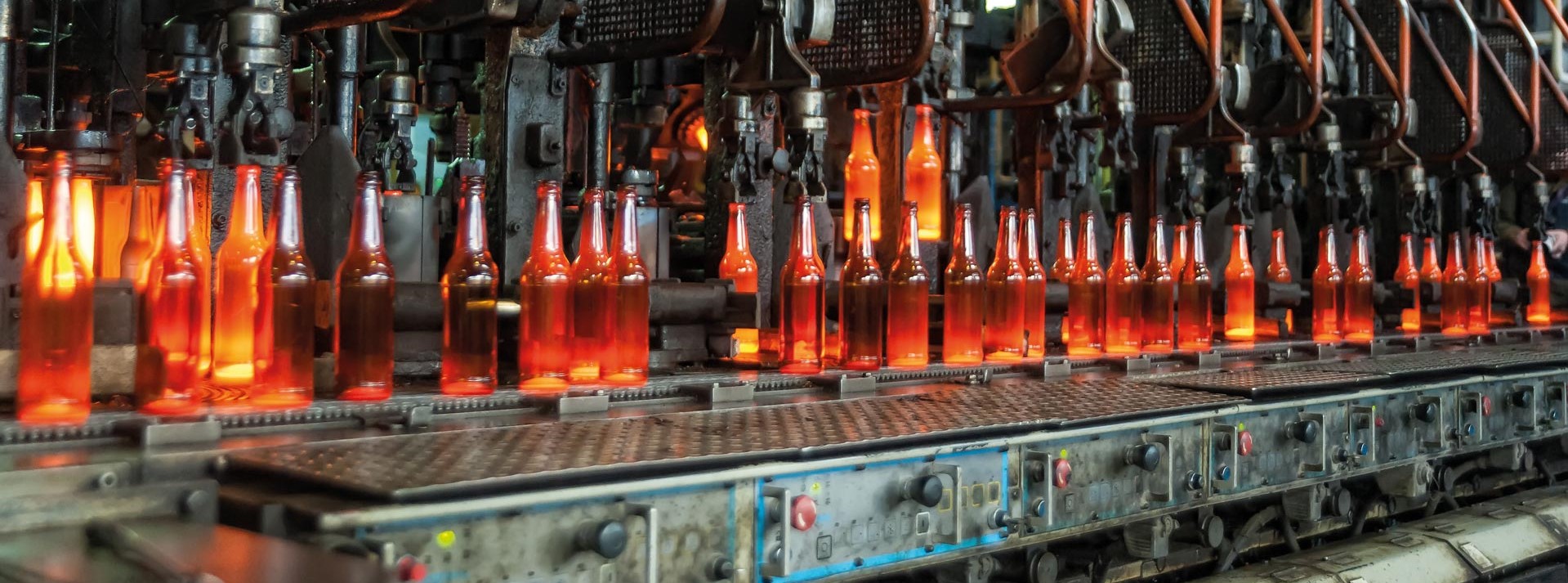
Servo Plunger integrated with DFS
System to automatically regulate the pressure profile (duration and pressure levels) of the proportional valves controlling the plunger up movement for PB productions, with the aim to:
- Equalize and keep stable the motion profile of each plunger mechanism to minimize container defect
- Keep stable the required pressing time to get homogeneous behaviors in dynamic environments
- Avoid over-pressures during the plunger up phase
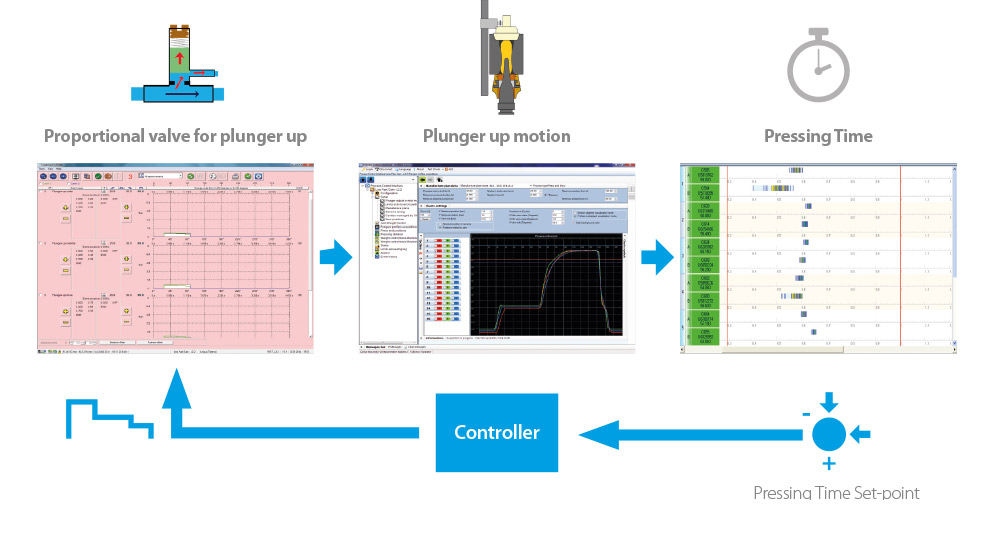
Bottero Proportional Valves 2.0
- Close loop on the output pressure based on a dedicated sensor
- Two valve types
- Possibility to electronically configure the valve type (flow or pressure)
- Complete mechanic retrofit with existing bases
- Same operator interface with control electronic
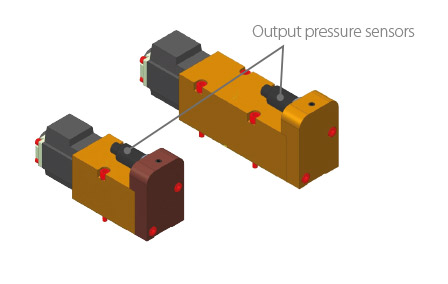
Multi Weight Manager Application
- Tool to support setup and control of productions with multiple weight articles
- Optional plug-in of Bottero servo feeder
- The variable gob weight is achieved regulating the plunger parameters of the servo feeder
- Capability to compensate glass accumulation phenomenon due to the return trajectory of the needles
- Commercial weight scales can be optionally integrated for automatic weight acquisition
- The tool can interwork with Tiama HOT mass, a camera system measuring speed and volume of the gob while falling, with the main objectives to automatically regulate the weight of the gob and to control its shape. This integration offers significant advantages compared to the other solutions:
- No need to manually weight the produced bottles
- No production losses due to manual weighting
- Possibility to setup multi-weight productions (at feeder level) while other operators change equipment at shop floor for the new jobs to be put in production. In this way, as soon as the IS machine is ready for production, the multi-weight gob setup is already up-and-running.
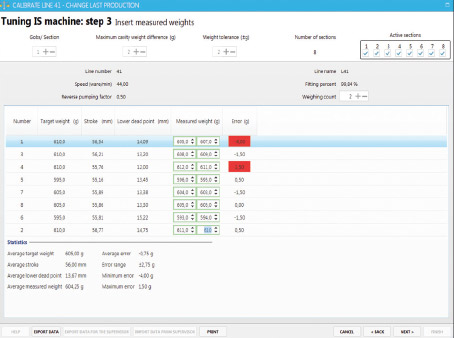
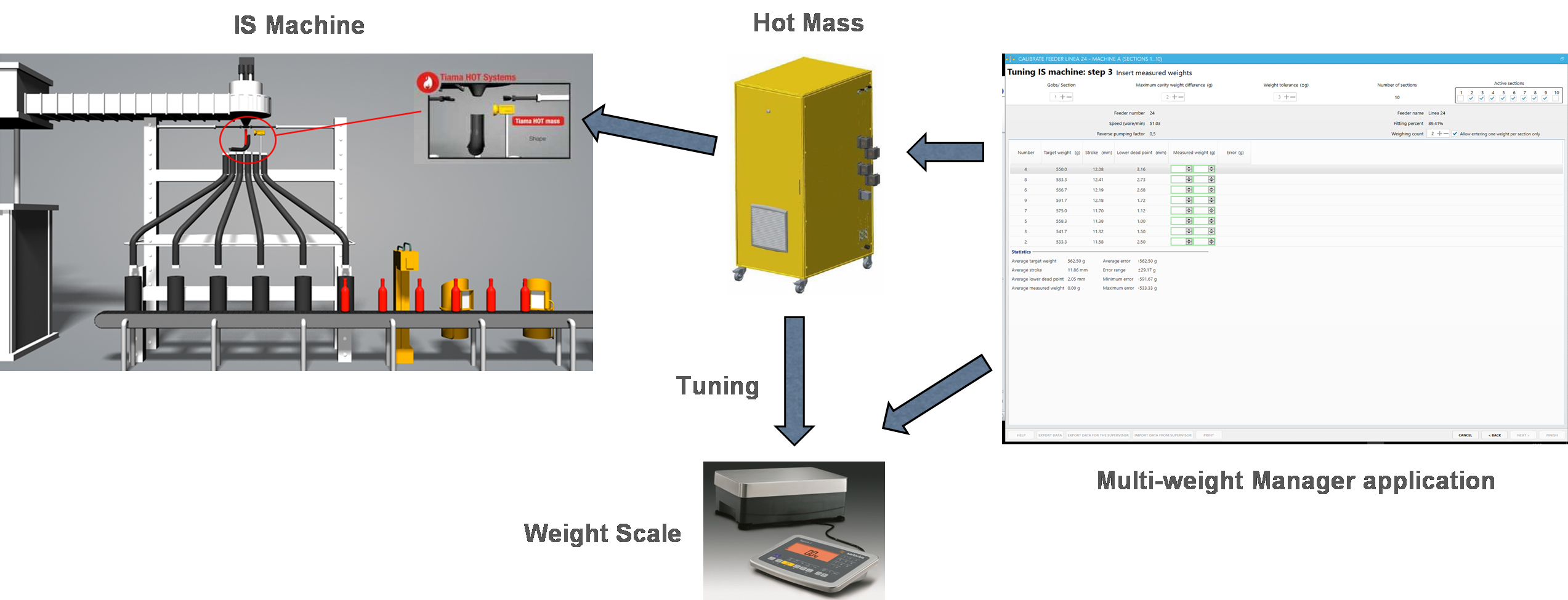
Process View close-loop controls
The ‘’process-view close loop control’’ represents a key evolutionary step: from tier1 loops (in charge to control sub-processes) to systems looking at the forming process from a higher level perspective, of which BoX is a unique example, putting the produced containers at the center of the measuring processes at the Hot-End.
Looking at a complete hollow glass production line, from batch to palletizers, the essential element to control is the HE forming process: mastering the forming process is key to be able to control the overall production line.
The Box Platform
Automation platform implementing process monitoring and automation functions related to:
- Automatic control and optimization of ware spacing
- Automatic control and optimization of vertical glass distribution (VGD)
Evolution of the BoX concept
The roadmap towards a predictive model of the production process

Big Data Analysis
The Big Data approach has the purpose to analyze measurements and data to learn the optimal process behavior, in particular:
1. Identify the key process parameters that most affect the final results in terms of:
- Correlation between HE data measurements (gob and parison data, IR measures, …)
- Geometrical characteristics of containers (weight, shape, verticality, etc.)
- Glass thickness distribution
- Major defects
2. Find out the optimal correlation between HE and CE data and measurements
Machine Learning: definition of the process model
The Process Control system receives as input HE data and implements automatic corrections to the settings of the IS machine, according to the parameters of the correlation model coming from the Big Data Analysis.As soon as CE measurements are available, the Machine Learning box adjusts and optimizes such model parameters according to the dynamic characteristics of the operational environment.